Purdue Lean Six Sigma Green Belt Case Study Notes: A Comprehensive Guide to Mastering the Process
Are you considering earning your Purdue Lean Six Sigma Green Belt certification? Do you want to understand case study notes that will help you not only pass your exam but also excel in real-world process improvement projects? This detailed guide is designed to provide you with in-depth insights and practical knowledge for mastering the Purdue Lean Six Sigma Green Belt concepts and applying them effectively. Whether you’re aiming to advance your career or enhance your organization’s performance, this article will give you the tools and information you need to succeed.
What Is Lean Six Sigma?
Before diving into the specifics of Purdue Lean Six Sigma Green Belt case study notes, it’s essential to understand the Lean Six Sigma methodology and how it improves business processes. Lean Six Sigma is a powerful combination of two distinct approaches: Lean and Six Sigma. Both aim to improve processes by reducing inefficiencies, waste, and variability, but each focuses on different aspects.
Lean Principles
Lean focuses on eliminating waste (also known as muda) to create more value with fewer resources. Waste can be in the form of excess inventory, unnecessary motion, waiting times, or overproduction. The key principle of Lean is to streamline processes and create more efficient workflows. Lean’s main goal is to speed up processes while maintaining or improving quality.
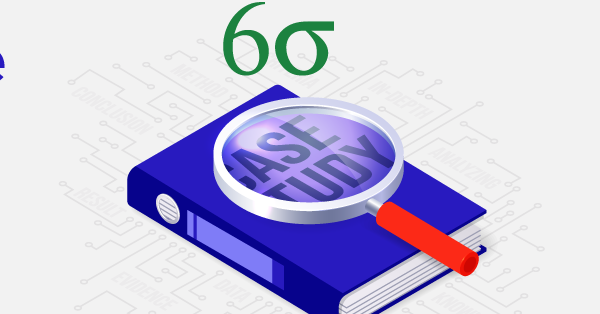
Six Sigma Principles
Six Sigma, on the other hand, focuses on reducing variation and defects in a process to ensure that it meets customer expectations. Using statistical methods, Six Sigma seeks to identify the causes of variation and eliminate them. A process that operates at Six Sigma quality produces fewer than 3.4 defects per million opportunities, meaning it is highly reliable.
By combining these two methodologies, Lean Six Sigma helps organizations achieve high levels of efficiency, quality, and customer satisfaction.
What Is the Purdue Lean Six Sigma Green Belt Program?
The Purdue Lean Six Sigma Green Belt certification is an internationally recognized program that trains individuals in process improvement techniques. Purdue University is known for its commitment to academic excellence, and the Lean Six Sigma Green Belt certification they offer is highly respected.
The Green Belt certification is a valuable credential for professionals who want to contribute to process improvement projects within their organizations. It’s particularly useful for employees who are part of teams that focus on optimizing operations, increasing efficiency, and improving quality.
Participants in the Purdue Green Belt program learn practical skills in project management, data analysis, and process optimization. This program prepares individuals to take a leadership role in process improvement efforts and equips them with the tools needed to implement change successfully.
Also Read: Monica Swanson Realtor Alabama EXP: A Comprehensive Guide
Why Choose Purdue Lean Six Sigma Green Belt Program?
The Purdue Lean Six Sigma Green Belt program offers several advantages for individuals and organizations. Some of the key benefits of pursuing this certification include:
1. High-Quality Training
Purdue University’s program provides rigorous training based on the latest Lean Six Sigma practices. The program offers a blend of theoretical knowledge and practical, hands-on exercises that help you apply what you’ve learned to real-world scenarios.
2. Real-World Case Studies
The program includes case studies that reflect the challenges organizations face in various industries. By working through these case studies, students gain valuable experience in tackling process improvement challenges and can apply the principles of Lean Six Sigma directly to their work.
3. Global Recognition
A Purdue Lean Six Sigma Green Belt certification is highly respected in the global market. Whether you’re working in manufacturing, healthcare, or service industries, this certification is recognized as a mark of excellence in process improvement and project management.
4. Career Advancement Opportunities
Achieving Green Belt certification opens doors to career advancement. Many organizations are looking for professionals who can drive operational efficiency and improve processes. Lean Six Sigma certifications, especially from a prestigious institution like Purdue, help demonstrate your value as a problem solver and leader.
Key Lean Six Sigma Green Belt Concepts to Master
To effectively tackle Purdue Lean Six Sigma Green Belt case study notes, you need to understand the fundamental concepts that form the backbone of Lean Six Sigma. Let’s go over some of the most important topics that you will encounter during your training and certification.
1. DMAIC Methodology: The Core Framework of Lean Six Sigma
At the heart of Lean Six Sigma is the DMAIC methodology, which stands for Define, Measure, Analyze, Improve, and Control. This structured approach is used to identify and solve problems in processes.
Define
In the Define phase, you identify the problem you are trying to solve, establish the project goals, and understand the customer’s requirements. The goal is to create a clear problem statement and ensure that everyone involved in the project is aligned on the objectives.
Also Read: Lean Six Sigma Project at Urgent Care Center: A Pathway to Operational Excellence
For example, in a Purdue Lean Six Sigma Green Belt case study, the Define phase might involve identifying inefficiencies in a customer service process and gathering input from key stakeholders to set goals for reducing wait times and improving customer satisfaction.
Measure
In the Measure phase, you gather data on the current state of the process. This phase involves identifying key metrics and collecting data to evaluate the performance of the process. It is essential to have accurate data to assess the extent of the problem.
For example, a case study might require you to collect data on the number of customer complaints, average wait times, and service times to get a clearer picture of process performance.
Analyze
During the Analyze phase, you identify the root causes of problems using data analysis tools. This is where statistical tools like Pareto charts, fishbone diagrams, and scatter plots come in handy. You analyze the data to determine which factors are contributing to inefficiencies or defects in the process.
For example, the Analyze phase of a case study could involve performing a root cause analysis on why customer service representatives are taking longer to resolve issues. By examining data trends, you may find that outdated technology or poor training is contributing to the delays.
Improve
In the Improve phase, you implement solutions to address the root causes identified in the previous phase. This may involve redesigning processes, automating tasks, or introducing new technologies to improve efficiency.
A case study example could involve recommending the adoption of a new customer service software that speeds up response times and helps resolve customer queries more effectively.
Control
The Control phase involves ensuring that the improvements are sustained over time. This includes monitoring the performance of the process, creating control charts, and implementing standard operating procedures to maintain the improvements.
In the context of a case study, this might involve setting up a monitoring system to track customer satisfaction over time and ensuring that the improvements are maintained by regular training and feedback loops.
2. Process Mapping and Flowcharts
A significant part of Lean Six Sigma involves visualizing processes to identify inefficiencies. Process maps and flowcharts are tools used to document and visualize how work flows through a process. These tools help you see where delays, bottlenecks, or waste are occurring.
Process mapping is crucial in case study notes, where you’ll be asked to draw process maps and identify potential areas for improvement. By visualizing the process, you can easily spot inefficiencies and design a more streamlined approach.
Also Read: Sapiens Adaptik Platform Development Software: A Comprehensive Guide
3. Statistical Tools for Data Analysis
Data analysis is at the core of Lean Six Sigma. Green Belts learn to use a variety of statistical tools to interpret data and assess the effectiveness of improvements. Some of the key statistical tools include:
- Histograms to understand the distribution of data
- Control charts to monitor process stability over time
- Pareto charts to identify the most significant problems
- Regression analysis to determine relationships between variables
These tools are essential for understanding how a process behaves and identifying the areas that need the most attention.
4. Root Cause Analysis
A crucial part of Lean Six Sigma is determining the root causes of problems. Root Cause Analysis (RCA) is a systematic approach used to identify the underlying causes of issues. It helps you move beyond symptoms and address the real problem.
Tools for root cause analysis include the Fishbone diagram (Ishikawa diagram), 5 Whys technique, and Failure Mode and Effects Analysis (FMEA). These tools help you ask the right questions and dig deeper into issues to find solutions.
Real-World Applications of Purdue Lean Six Sigma Green Belt
Understanding the concepts is only part of the equation; you must also apply them in real-world situations. The Purdue Lean Six Sigma Green Belt case study notes provide valuable examples and practice in applying the methodology to different industries. Let’s explore how Lean Six Sigma Green Belts are making an impact in various sectors.
1. Manufacturing
In manufacturing, Green Belts often work on improving production processes. By eliminating waste and reducing defects, Lean Six Sigma can significantly enhance operational efficiency. For example, a Green Belt might identify inefficiencies in the assembly line and work to reduce cycle times, improve quality control, and minimize downtime.
2. Healthcare
In the healthcare sector, Lean Six Sigma can be used to improve patient care and reduce wait times. Green Belts might focus on streamlining patient flow in hospitals, ensuring that patients receive care faster, and reducing errors in medical treatments.
For instance, a Purdue Lean Six Sigma Green Belt case study might involve improving the patient intake process by eliminating unnecessary steps and automating certain tasks. This can reduce the time patients spend waiting and improve overall patient satisfaction.
3. Service Industries
In service industries, Lean Six Sigma Green Belts help improve customer experience by reducing delays and enhancing the quality of service. By analyzing service delivery processes and identifying bottlenecks, Green Belts can suggest improvements that result in faster response times and better customer satisfaction.
Also Read: Krugh Alexander Attorney Houston: A Comprehensive Guide to Legal Expertise
FAQs about Purdue Lean Six Sigma Green Belt Case Study Notes
What is the main objective of Purdue Lean Six Sigma Green Belt certification?
The primary goal of the Purdue Lean Six Sigma Green Belt certification is to equip professionals with the knowledge and tools necessary to improve processes, eliminate waste, reduce defects, and enhance operational efficiency within organizations.
How do case study notes help in preparing for the certification exam?
Case study notes provide practical examples that allow you to apply the Lean Six Sigma principles in real-world scenarios. They help reinforce theoretical knowledge by showing how it can be used in problem-solving and process improvement projects.
What are the prerequisites for pursuing the Purdue Lean Six Sigma Green Belt certification?
While there are no strict prerequisites for the Purdue Lean Six Sigma Green Belt certification, a basic understanding of process management and some experience in business operations can be beneficial.
How long does it take to complete the Purdue Lean Six Sigma Green Belt program?
The program typically takes several weeks to complete, depending on your pace. Purdue offers both online and in-person courses, so you can choose the format that best fits your schedule.
What tools will I learn to use as part of the Green Belt certification?
As part of the Purdue Lean Six Sigma Green Belt program, you will learn to use a variety of tools, including statistical software, process mapping tools, control charts, and root cause analysis methods. These tools are essential for analyzing data and implementing process improvements.
Conclusion
The Purdue Lean Six Sigma Green Belt certification is a valuable credential for anyone seeking to improve their organization’s efficiency, quality, and customer satisfaction. Mastering the core concepts, such as DMAIC, process mapping, data analysis, and root cause analysis, will give you the tools you need to tackle real-world process improvement challenges.
By understanding and applying Purdue Lean Six Sigma Green Belt case study notes, you can gain practical experience in problem-solving and process optimization. Whether you’re in manufacturing, healthcare, or service industries, Lean Six Sigma can help you streamline processes and deliver better outcomes. With this guide, you now have the knowledge and insights needed to excel in the certification program and make a significant impact in your organization.